main
We are committed to delivering transformative solutions for our
customers, employees, business partners, and communities
We believe in bold action and innovation to create a socially, environmentally,
and economically sustainable tomorrow
Newsroom
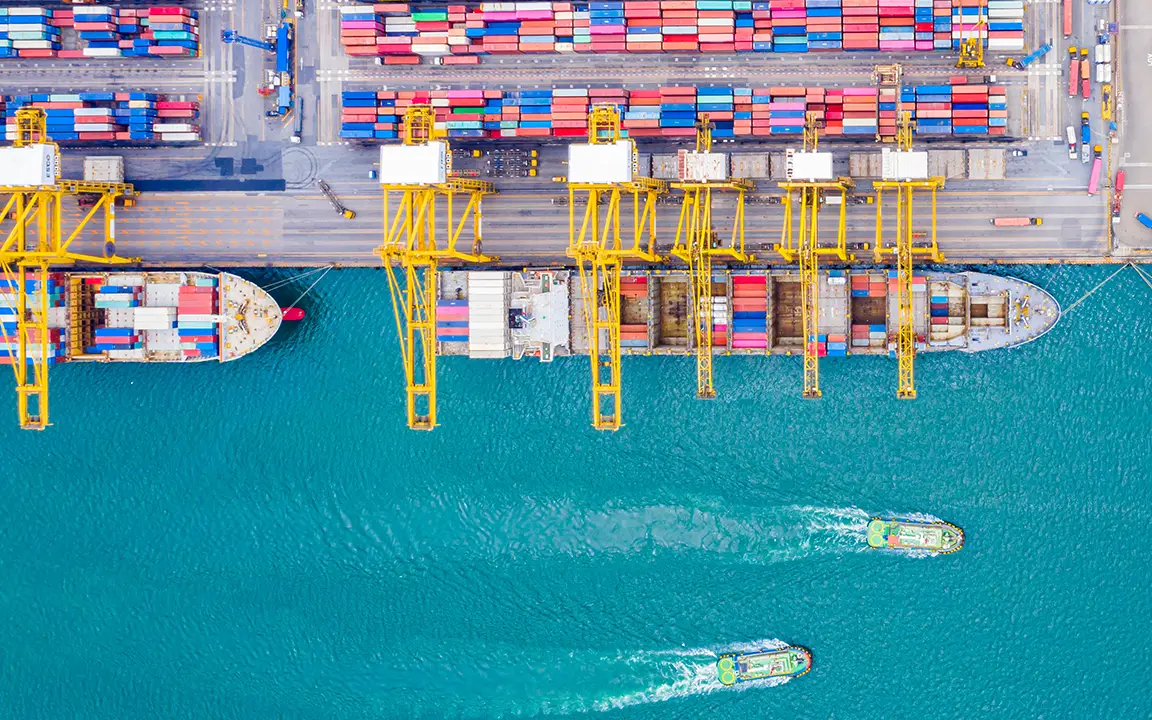
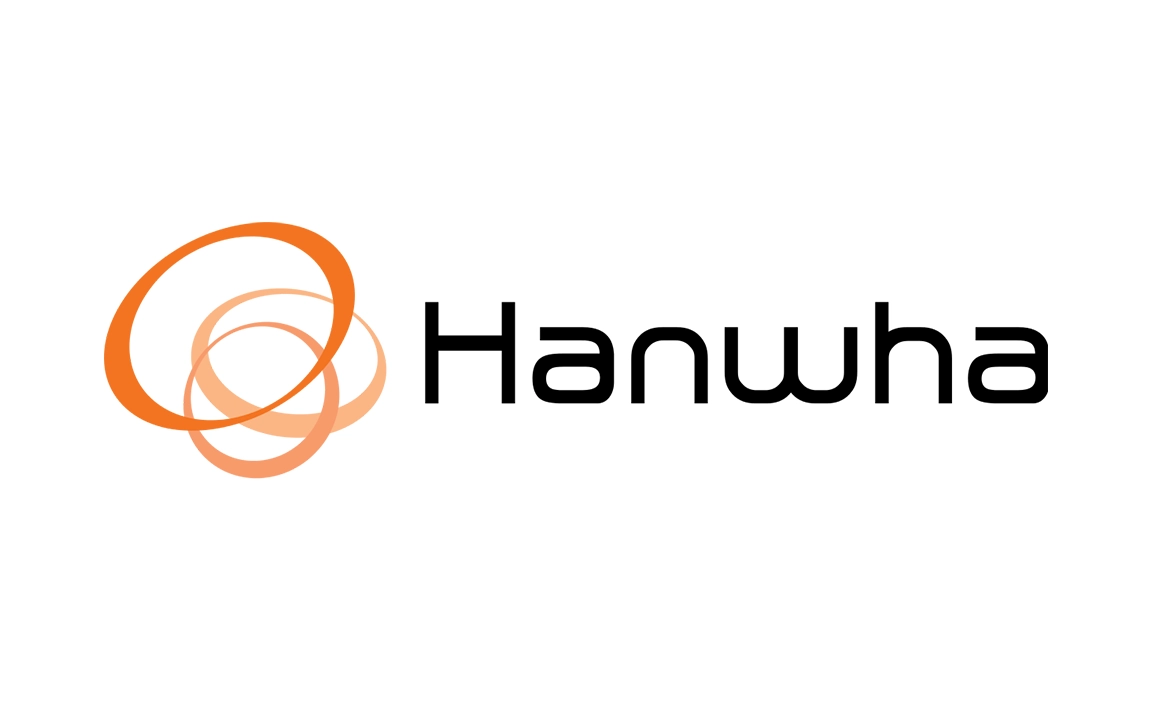
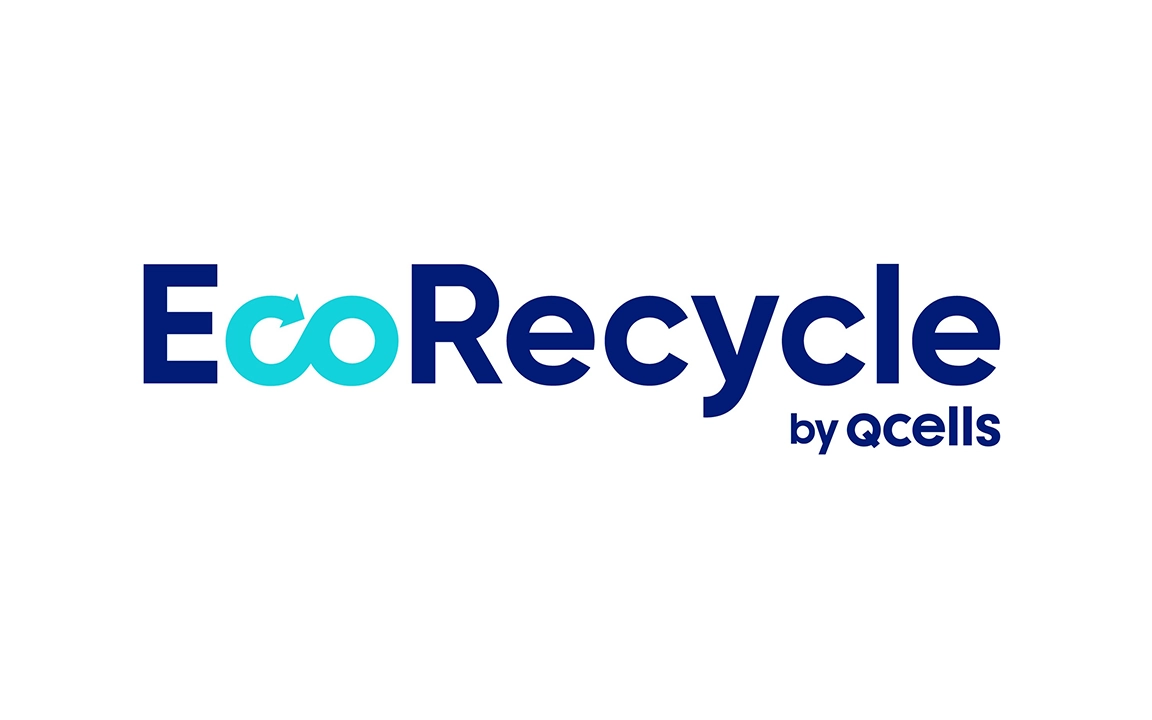
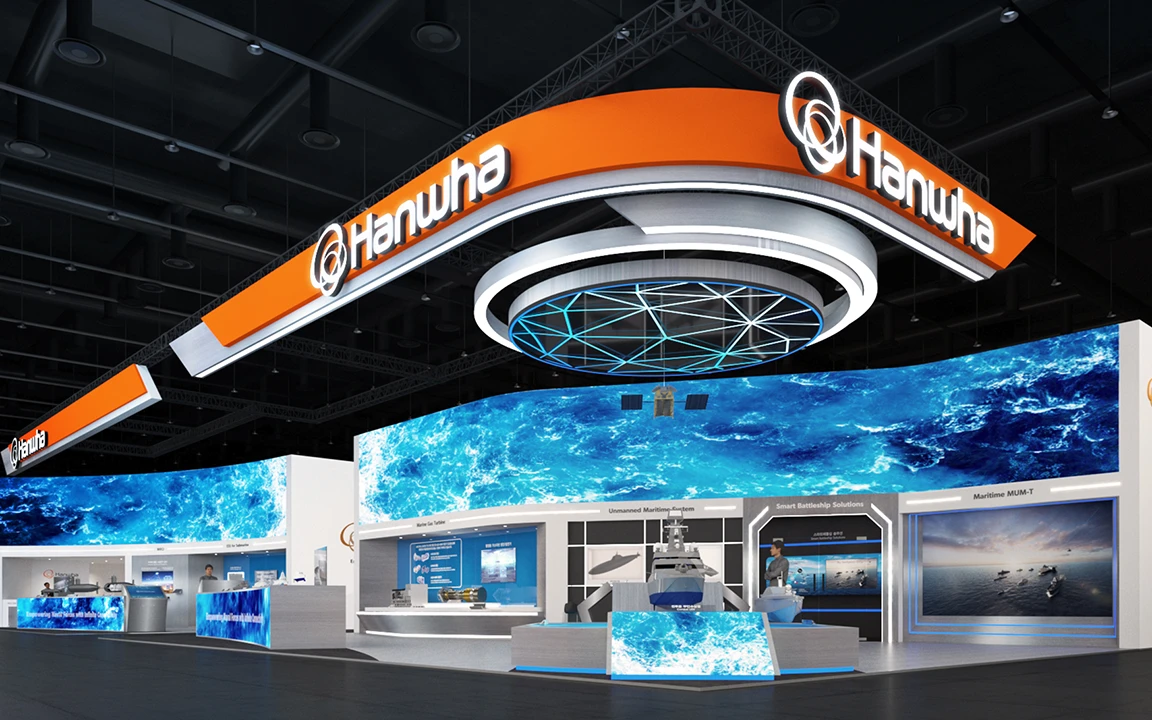
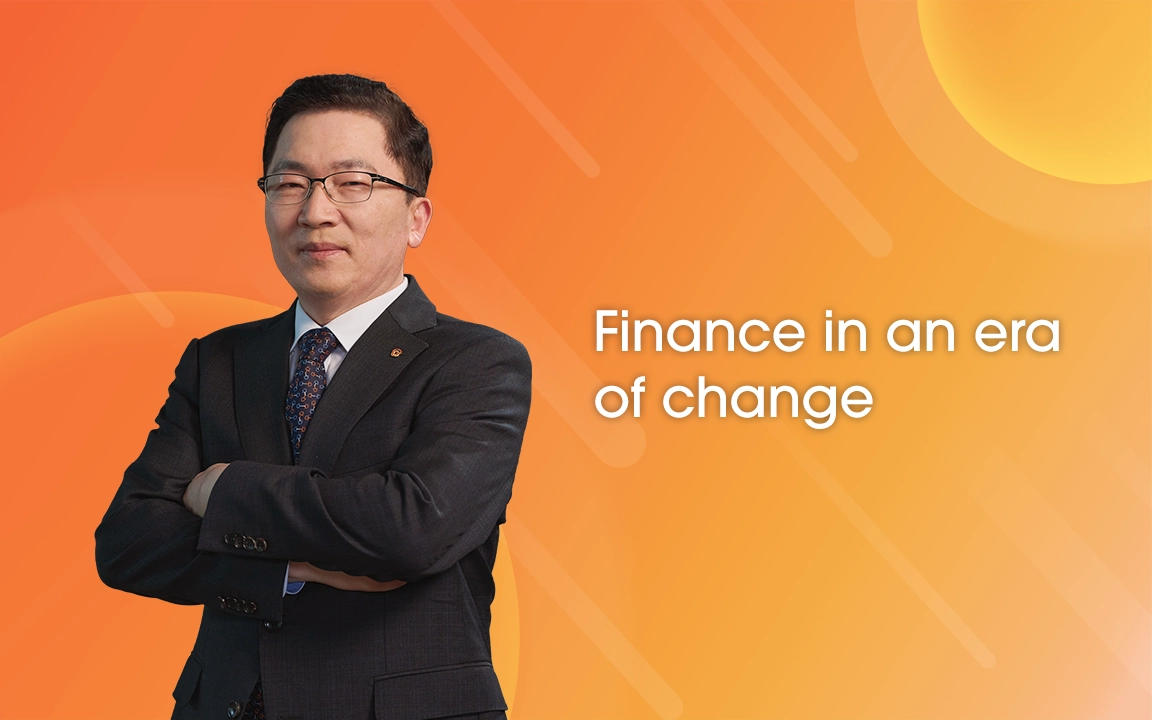
We deliver
future-ready solutions and
impactful innovations worldwide
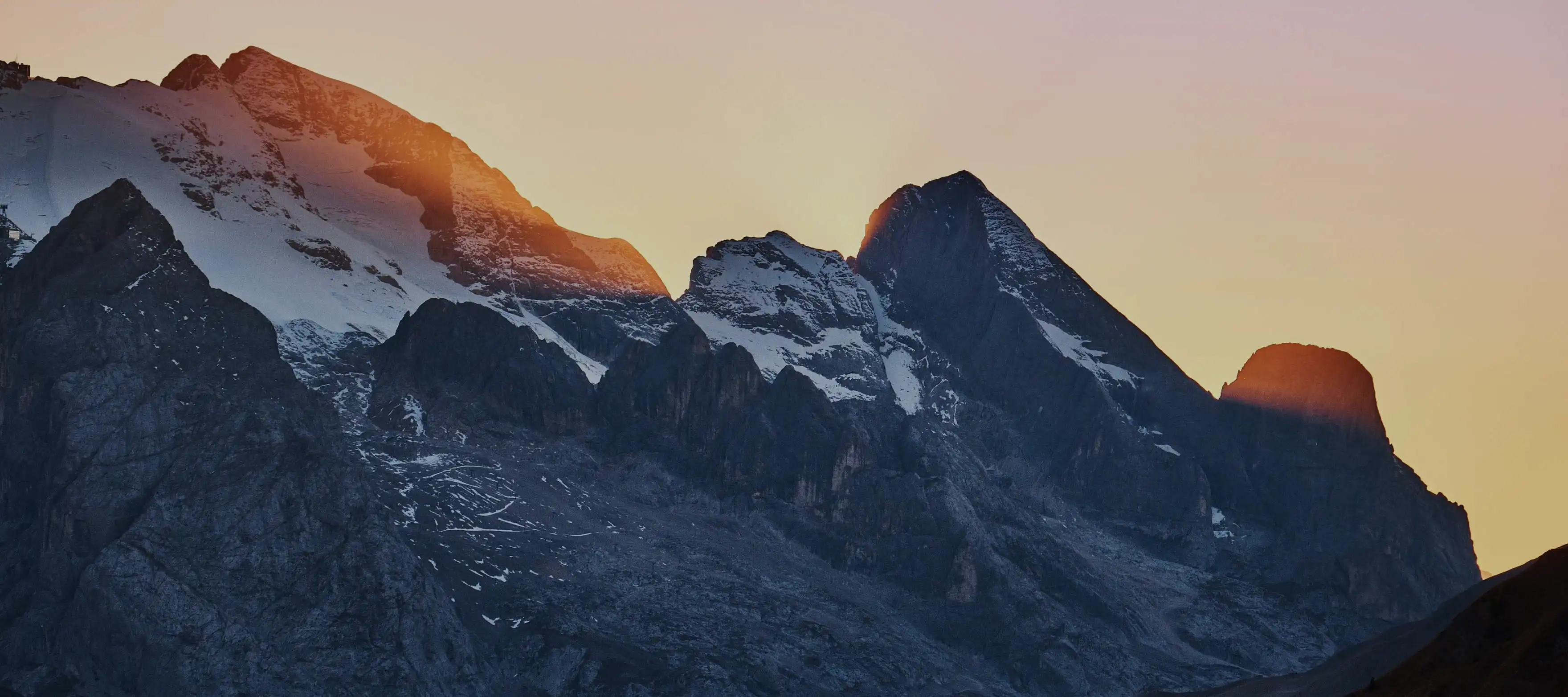
Our Brand Purpose
A relentless commitment to sustainability drives
our bold innovation, allowing us to create
transformative solutions for individuals, society, and the planet
Our Brand Values
-
Sustainable and
Inclusive GrowthWe strive for social, economic, and
environmental prosperity for all
-
Technology and
Solution-driven InnovationThrough technological innovation,
we provide solutions from people to planet
-
Enhancing
LivesWe lay the foundation for a fulfilling life through
our technologies, products, and services
Global Reach,
Global Impact
As our operations continue to expand
across continents
and communities,
we are able to deliver more solutions to meet
your needs no matter where they are